Ten With Tom: Abraham Moon & Sons

Steam bent oak wood and sustainably sourced wool harmoniously unite to create our popular upholstered furniture collection. But where does the upholstery actually come from? And why wool?
As one of our trusted, sustainable suppliers of superior-quality upholstery, we've caught up with Martin Aveyard (Creative Director at Abraham Moon with 45 years of knowledge under his belt) to find out more about the brands woollen fabric range, the way their business operates sustainably and what it's like to work from the oldest vertical mill in the UK.

Tell us a bit about how Abraham Moon & Sons started?
MA: "It was our founder of the same name who started our journey in 1837, providing yarns to local weavers in Guiseley, Yorkshire, before selling the fabrics at the bustling Leeds cloth markets. Our first three-storey factory was completed in 1868 and remains on the same spot to this day, albeit rebuilt after a fire in 1902.
We’re now one of Britain’s last remaining vertical woollen mills, which means we complete all parts of the process from natural wool to finished fabric on a single site".
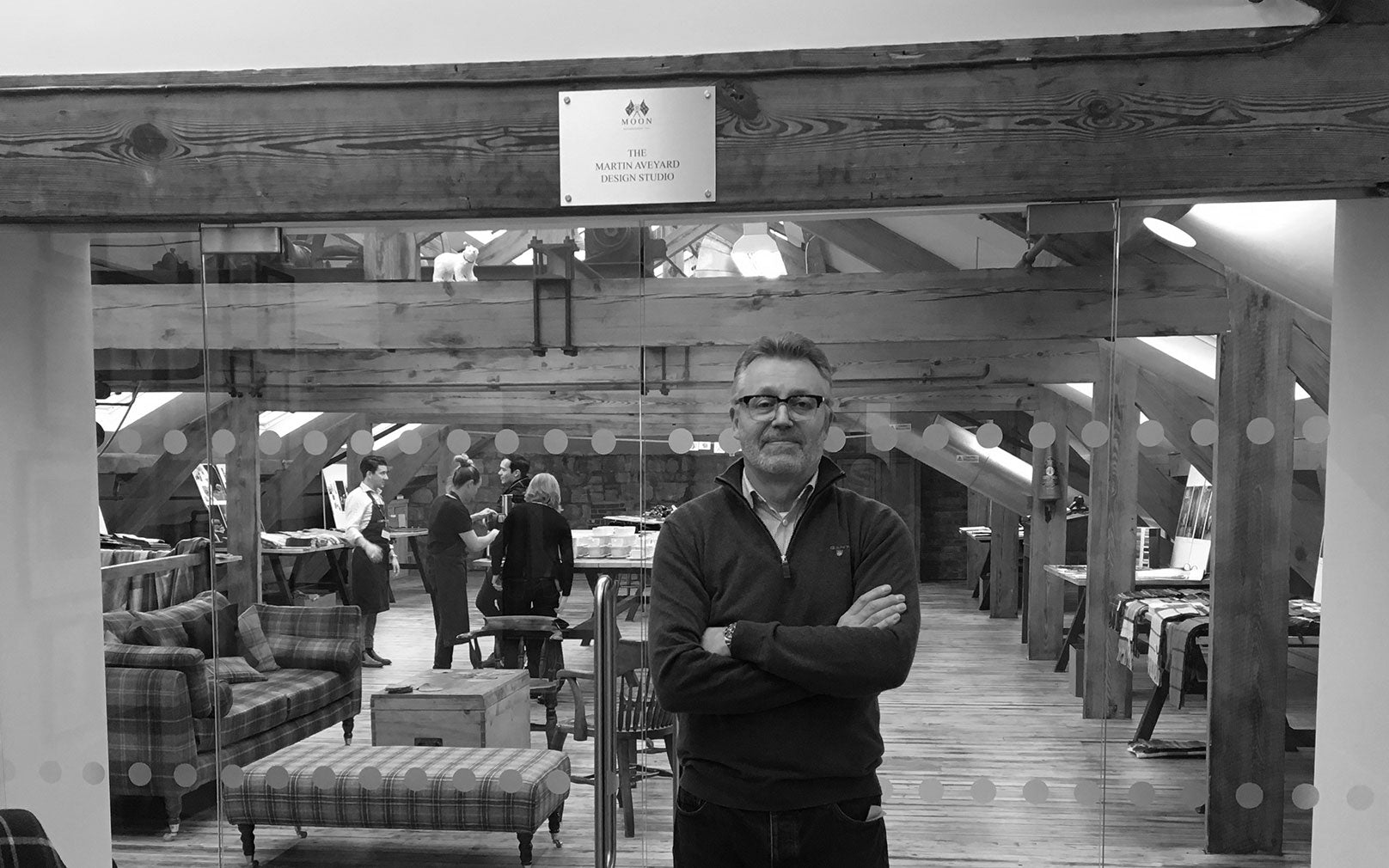
What key processes happen at your mill? How do you turn wool into your beautiful, superior quality fabrics?
MA: "There are eight key processes in the making of our fine wool fabrics. First up are dyeing and blending. We can dye in any one of 500 individual shades using different combinations of dye, water, pressure and temperature, before mixing precise quantities of these dyed wools to create a blend of between 2-7 colours. These blends are unique to our fabrics, giving them richness and life that can't be achieved by using just a single dye alone.
After the wool is blended it moves through 'carding', a series of combs & rollers which uniformly draws out the fibres. Next follows spinning where the threads are twisted to create a thin but strong yarn ready to be woven".


"The warping and weaving processes follow next, and this is the first time in production at which the final design becomes apparent. Warping aligns all of the vertical elements of a pattern in their precise order, before the weft (horizontal thread) is added in loom to create full pieces of woven fabric.
The final two steps following weaving are scouring (washing) and steam pressing; combined this is known as ‘finishing’. We scour our fabrics in pure Yorkshire spring water pumped from boreholes 800ft below our factory giving it a unique, soft handle. Steam pressing sets the finish in place, and after in-depth quality checks are completed, the fabric is ready to be sent to our customers."




What are your favourite qualities of wool?
MA: "My favourite wool would be Shetland, used for Moon furnishing fabrics - all of which is sustainably sourced and traceable all the way back to the individual farms from which it originated. The micron of this particular type of “cross-bred” wool is such that it provides an ideal balance between softness and durability. Aesthetically, the wool lends a richness of colour as you can see the individually dyed fibres blends in the final fabric".


What inspires your new collections?
MA: "Our history is obviously a vital part of what makes Moon, Moon. Our reputation has been forged through our UK heritage, quality and design. I have always found my personal design inspiration very difficult to define, the ideas just evolve over time – long periods of reflection and experimentation followed by brief periods of a very clear direction and selection process. I have never been one to focus on what else is on the market or what any perceived competitors may be doing. This has enabled us to bring something different to the market with our distinctive and, at the time, unique checks.
I believe it starts with understanding the big picture – looking, listening and absorbing many influences and then having the enthusiasm to translate those ideas into a contemporary and commercial product which reflects the DNA of Moon. We also have a comprehensive archive of past designs dating back over 100 years should inspiration be required, though we are very careful not to overplay the heritage card. Trends in apparel generally move more quickly than interiors and though not always the same, the underlying direction helps us anticipate what may happen in fabrics for interiors".
Describe your typical working day(s)…
MA: "As you will imagine my typical working day has changed dramatically in the last year due to Covid. No travelling at home or abroad to visit trade shows, customers, or our various agents worldwide. The discussions, feedback and general face-to-face communication with our customers and agents from around the world is something I greatly miss, particularly as many have become close friends over the years.
My job, however, is very difficult to do from home so whilst many of my colleagues have been working from home, I am generally found at the mill. Fabrics have to be seen and touched and as we have continued to keep manufacturing throughout the pandemic, I also need to be at hand for a myriad of reasons related to the technical experience I’ve gained over the years".

What’s your favourite part of your job?
MA: "The favourite part of my job is the journey from visualising a concept to overseeing the technicalities of designing, then creating a finished product. It's a brilliantly creative process. My only restrictions are those of the limitations of our machinery or my imagination but in the end, I have to create a product that people want to buy.
The most rewarding part of my job, however, is when I see where our products end up. Whether worn by the general public, or celebrities from Justin Bieber and Boris Johnson to Royalty. Clothing made from our fabrics, scarves, throws and furnishings appear in films, on the telly, in hotels, pubs, clubs, restaurants and many other applications– even cars".

Why is sustainability important to your business?
MA: "Today it`s not enough just to make a beautiful item. Customers (thankfully) want to know the back story of where and how it was made. Sustainability runs through everything we do at Moon, from the inherent natural benefits of the wool itself right through to developments in our Yorkshire-based mill. Wool is naturally biodegradable in a short time frame (as little as three months) and is renewable too, with sheep of course growing a new fleece every year. For interiors, a 100% wool fabric is even more of a blessing, offering amazing insulation properties and working in harmony with its environment to absorb and not re-emit harmful pollutants from internal air.
The wool used for Moon furnishing fabrics is all sustainably sourced, traceable all the way back to the individual farms from which it originated. These farms agree to regular independent auditing under a strict set of criteria, the most important of which is to observe the five animal freedoms.
Within our factory, we have worked hard over the past decade to improve our energy efficiency and reduce our waste. Key investments in modern machinery and on-site solar power (providing up to 10% of our energy) will help us to continually reduce our carbon footprint, while any excess from our production process such as the woven selvedge is sent to other manufacturers to recycle and re-use. This ‘scrap’ wool can be found in useful products such as insulation, felted wools and carpeting underlay".

What would you consider the brand’s biggest achievement to date?
MA: "Introducing and promoting the innate and beautiful qualities of wool as a fabric for interiors to a wider audience. When we launched our first collections approx. 15 years ago our customers perceived wool as being “itchy and scratchy” however, once they tried it they were converted and we never hear those comments today".
Which fabric would you pair with one of our upholstered furniture designs to create a bespoke piece?
MA: "I would choose the Arbor Armchair in SKYE/Burnt Orange. This design has become our signature check, still a best seller 15 years after its introduction. The SEA colour way is regularly seen in the press, having now graced the bottoms of three Prime Ministers in number 10 Downing Street".

What do the next six months hold for you?
MA: "Although our apparel business has suffered during lockdown, our furnishings and throws have been quite buoyant. As people have been spending more time at home and have been unable to socialise there has been little need for more formal clothing, but more time to reflect on their décor or maybe appreciate the cosy comfort of a nice wool throw. We believe that once we get back to some kind of normality there will be pent up demand for the more tailored clothing that - quite honestly - there has been no need to buy recently.
As far as interior trends are concerned post pandemic they can be viewed in two ways. The main and underlying trend has been a return to nature and the pandemic only exacerbated this. Inspiration from nature, organic shapes, and the calm relaxation of a palette of natural colours – neutrals, greens and brown wood tones. In this environment spending much more time at home bright details can begin to annoy. Conversely, it may be that we are looking forward to a better, brighter future – quite literally when it comes to design - and expecting fresh ideas and fearless colours and textures".

Posted: 26.02.21
Updated: 23.04.25